Spring is Here!!
- B2D2
- May 13, 2020
- 2 min read
Hello everyone! Now with the Walpurgis night past us, spring has officially begun. Even with the covid-19 situation still ongoing this is a reason for happiness. This week, we have prepared a spring-related subject as a follow-up of the satellite boom post: The tape springs!
These springs made of composite materials are developed at KTH and constitute a key part of the entire experiment. As described in our last post, they not only determine the structural integrity of the boom but also provide its deployment force. Our FFU's deployable boom systems is therefore purely mechanical whereas most other boom systems rely on electrical solutions. So why are we using such a boom mechanism? Mainly because the magnetic sensors should not be surrounded with electrical components since they can cause electromagnetic disturbances which would be detected by the sensor. An additional goal is to demonstrate how such a mechanical boom system can be used for small-sized satellites.
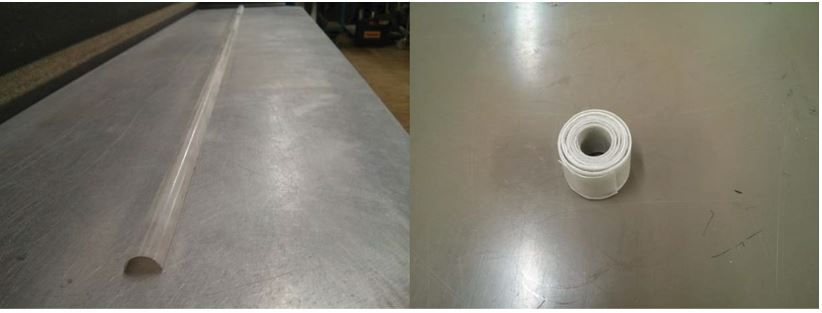
(credit: Jakob Ekelöw, Design and manufacturing of thin composite tape springs, KTH Stockholm 2014)
How exactly do they make the boom deploy? Well, consider an ordinary object such as a fork for example. By bending it the fork will deform, elastically or plastically, or even break if bending is too strong. In case of elastic deformation, the fork will retrieve its initial, stable shape after releasing the bending force. Most objects have only one of such a stable configuration, but our tape springs have two; The coiled and the straight configuration. However, in straight configuration the springs are more stable and hold the more favourable shape. This means that as soon as one segment or a part of a tape gets set off from the coiled state (e.g. the end of the coiled tape gets straightened) the nearby segments receive enough tension to start transferring to straight configuration as well. As a result, the tape springs are unrolling themselves from coiled configuration. Any object light enough and attached to the coil axis will get pushed away from the end of the tape spring. There we have the required deployment force.
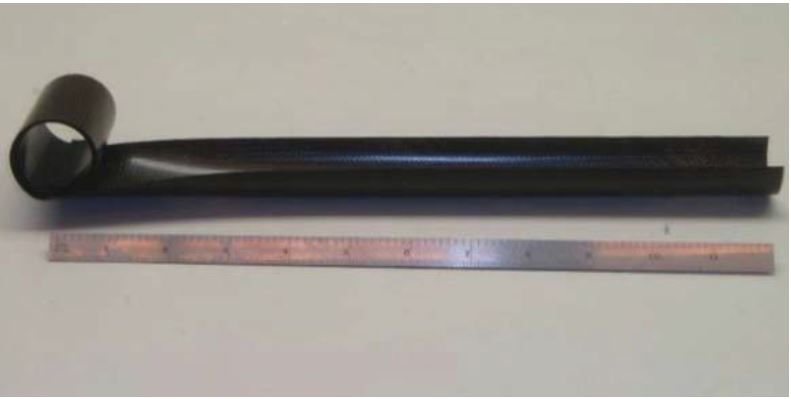
(credit: Jakob Ekelöw, Design and manufacturing of thin composite tape springs, KTH Stockholm 2014)
The property of having two stable states is obtained from the material characteristics and the manufacturing process of the tape springs. Multiple fibre-reinforcement layers are arranged to a well defined, structured tapes which are imbued with a specific polymer resin. These composite tapes then have to be cured while being spanned over a cylindrical pipe. This will later ensure the springs to have the more favourable configuration when straightened out. The second stable state is comes from the mechanical structure of the composite material.
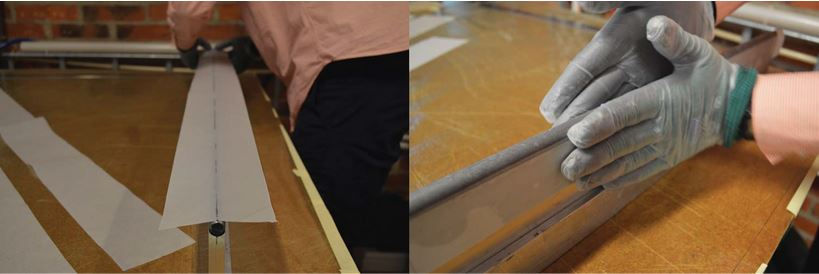
(credit: Jakob Ekelöw, Design and manufacturing of thin composite tape springs, KTH Stockholm 2014)
So far, these tape springs have shown exciting performances together with boom prototypes and are encouraging further applications in space technology. Our work now consists of the optimisation of both tape spring design and boom mechanism. Stay tuned for more!
I hope you liked the insights in our work on the tape springs! There is much more to come, all available on www.b2d2.se, on Facebook, and on Instagram. Stay tuned for more infos on our test campaign!
Comments