Breakpoint
- B2D2
- Jul 5, 2020
- 2 min read
Hej everyone! Hope you are doing great!
So, this week we’ll talk about the hardships our experiment has to go through and how we can determine whether it will come out the other side victorious!
As you can imagine, being aboard a rocket during launch might be a rough experience. For that reason, we need to make sure that the components aboard can withstand the loads and won’t fail by suddenly breaking. A way to determine if the components are properly designed to withstand the loads is by performing a structural analysis. On this post we will focus on the Magnetometer Boom Assembly (MBA) structural analysis.
The first step is to recognize the loads that are going to affect the components. In this case the two main events that create loads on the boom are, the acceleration of the rocket while ascending and the spin of the rocket. The acceleration creates a load that points downwards, and the spin of the rocket creates a load that points outward.

After we have the loads, we can perform a structural analysis by using a Finite Element Analysis (FEA) program. Which is very helpful, since we don’t have to build everything, spend money and then realize that it’s not working as desired. So, we take our 3D CAD models, assign materials, and apply loads. Then the program, by applying the theory we study a lot to learn, does the several pages calculations we would have done by hand and gives us the results, safe from “forgot a minus sign somewhere” errors. We’ve all been there..
The results from a FEA program look like the figures below.
A very important outcome of the simulation are the displacements, the results can tell us how much the components will move around. If the displacement is too much or at a critical place, then we probably need to look through our design again. The displacement of the boom components can be seen in the figure below, the results are highly exaggerated, meaning that the values you see are in the scale of tens of micrometers. Clearances have been incorporated in the design of the boom at critical places so there are no issues with these results.
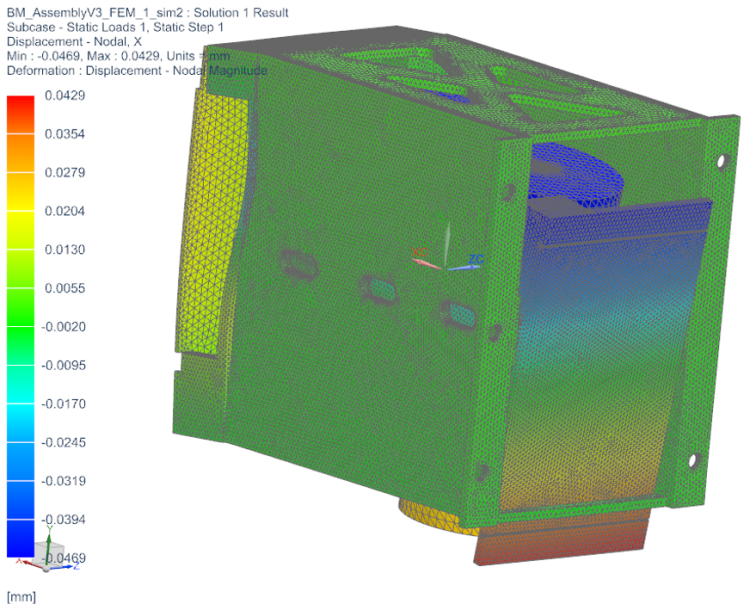
Another outcome from the simulation, are the stresses that result on our components due to the launch forces. We can compare the stresses with the maximum strength of the material it is made of and evaluate if we are safe flying this design. Ways of dealing with problematic stress values could be, thicken a plate or changing a material. In the image below we can see where the highest stresses are concentrated on the boom components.

Finally, after having the results of the structural analysis, we can determine whether we are safe to fly those parts or we go back make changes and repeat the procedure!
That was another one from me, take care and check out our website: www.b2d2.se, our Facebook page, and our Instagram accounts. Danai out!
Comments